This is Forward: Packaging
Leading the way in innovations
Togetherness is crucial in achieving our sustainability goals, by Jim Fox
Originally published in Holyrood on 4th March 2022
Glasgow’s hosting of the COP26 Conference last November put Scotland at the heart of global discussions around sustainability and emphasised the urgency with which we must act. There is now an expectation on government and businesses to deliver bold climate action over the coming months.
The Scottish Government has laid out its ambition to reach net zero emissions by 2045, and businesses have a role to play in realising this goal. At CCEP, we have committed to becoming a net zero business by 2040, leading the way in moving towards a cleaner, greener future for our business. As part of this we will be working closely with our supply chain partners to bring them with us on our journey.
Despite recent challenges, we’ve remained resolute in prioritising our environmental goals. For example, last year we introduced 100% recycled plastic (rPET) 500ml bottles across our core range, helping to save more than 29,000 tonnes of ‘new’ non-recycled plastic across our operations in Great Britain every year.
However, we know that we have a responsibility to go further and faster with our sustainability targets.
To have the biggest possible impact, industry needs to work together to ensure everyone is engaged in this mission, right along the value chain. CCEP is working towards an ambitious target of reducing carbon emissions across our value chain by 30% by 2030, and we are supporting 150 of our suppliers to help them set their own science-based net zero targets by 2023.
As part of this we led a 12-month collaboration between one of our longest serving logistics providers, MJD, and Green BioFuels. As a result, MJD has been able to transition to a Hydrotreated Vegetable Oil (HVO) biofuel across its fleet of haulage vehicles, cutting carbon emissions by 17,000 metric tonnes of CO2e per year.
We’re also determined to do more to increase the amount of quality recycled material we use in our packaging. The confirmation that the Deposit Return Scheme (DRS) in Scotland will go live in August 2023 is an important and welcome change. In support of Circularity Scotland, the designated scheme administrator, we’re working with all stakeholders to introduce a scheme that recycles our packaging and reduces our litter, as soon as we can. Our hope is that the implementation of the Scottish DRS will be recognized as best practice so that similar, interoperable schemes can be rolled out across the rest of the UK in a timely way.
We have a responsibility to protect the planet, but we also have a responsibility to deliver value for our customers. Increasingly the two are becoming intertwined – recent research showed 61% of consumers are making more environmentally-friendly, sustainable or ethical purchases, with 89% likely to continue this approach post-pandemic . That’s why we’re proud that our 500ml bottles are made with 100% rPET on our packaging at no additional cost to the consumer.
We are also closely involved in the Net Zero Pubs, Bars and Restaurants initiatives in association with Net Zero Now, the Sustainable Restaurant Association and Pernod Ricard UK. The programme is designed to help the hospitality industry to help address its greenhouse gas emissions by providing guidance on how to reduce carbon emissions, the actions needed to get there, and setting a standard against which they can be certified.
The example of DRS in Scotland demonstrates the transformative potential for environmental policy when government and industry work together. To meet broader sustainability goals, we must take the learnings from this collaboration and extend them to innovative ways of creating a better, greener future – together.
How our sustainability journey at Edmonton is helping to achieve net-zero, by Karl Probert
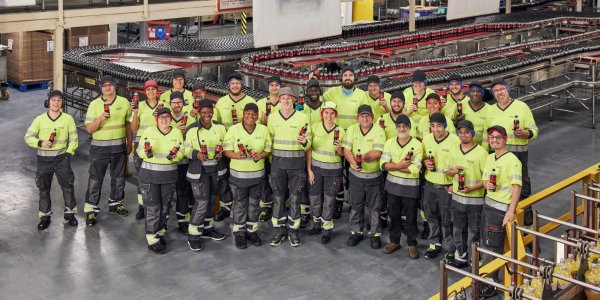
Originally published on PoliticsHome on 28th September 2022
The progress at our Edmonton site demonstrates the power of small changes in reducing carbon emissions.
This week we’ve reached an exciting milestone at our site in Edmonton by becoming the first Coca-Cola Europacific Partners (CCEP) factory in Great Britain to manufacture 500ml plastic bottles with attached caps across our brands.
The roll out marks the next step in our sustainability journey, following the initial switch to attached caps on our larger, 1.5L bottles earlier this year. The new design means that the lid will remain attached to its bottle, wherever it goes, preventing it from being discarded or thrown away separately. It will make it easier than before to recycle the entire bottle, ensuring that as much plastic as possible is making its way back to recycle and that no caps get left behind.
You’ll see the change across bottles of Coca-Cola Zero Sugar, Diet Coke, and Fanta Zero, initially in stores and outlets in the south of the country, with plans to implement the change across our entire range sold in Great Britain by the end of 2024.
It might sound like just a small change, but as a format designed to be enjoyed while out and about, it’s even more important that the caps stay attached to our 500ml plastic bottles, instead of ending up anywhere they aren’t supposed to. Combined with the fact that our bottles are 100% recyclable, and made from 100% recycled plastic* this amounts to a huge quantity of plastic being prevented from becoming waste, and instead being recycled, helping us drive towards achieving a circular economy.
The move forms part of our sustainability ambition, CCEPs This is Forward sustainability action plan, and helps us move one step closer to our all important 2040 net zero target.
A little goes a long way
All of this is happening from right here in Edmonton – our only site within the M25. We started production of our first 500ml plastic bottles with attached caps this week. In time, we’ll see the change rolled out across our other factory sites in GB including Sidcup and Wakefield. It really does show the power that small changes can have.
I like to think that this is something we know a lot about at Edmonton – the power of small changes.
We recently achieved a milestone 70% reduction in carbon emissions compared with 2010 levels. This is the result of many incremental steps at the site to increase efficiency, reduce waste and improve processes. We’ve been using 100% renewable electricity for over 10 years, including via a solar panel array on our factory roof, and we’ve not sent any waste to landfill for just as long. We also recently replaced all material handling equipment (MHE), such as forklift trucks, with new models powered by lithium-ion batteries, which produce no carbon emissions in their day-to-day operations.
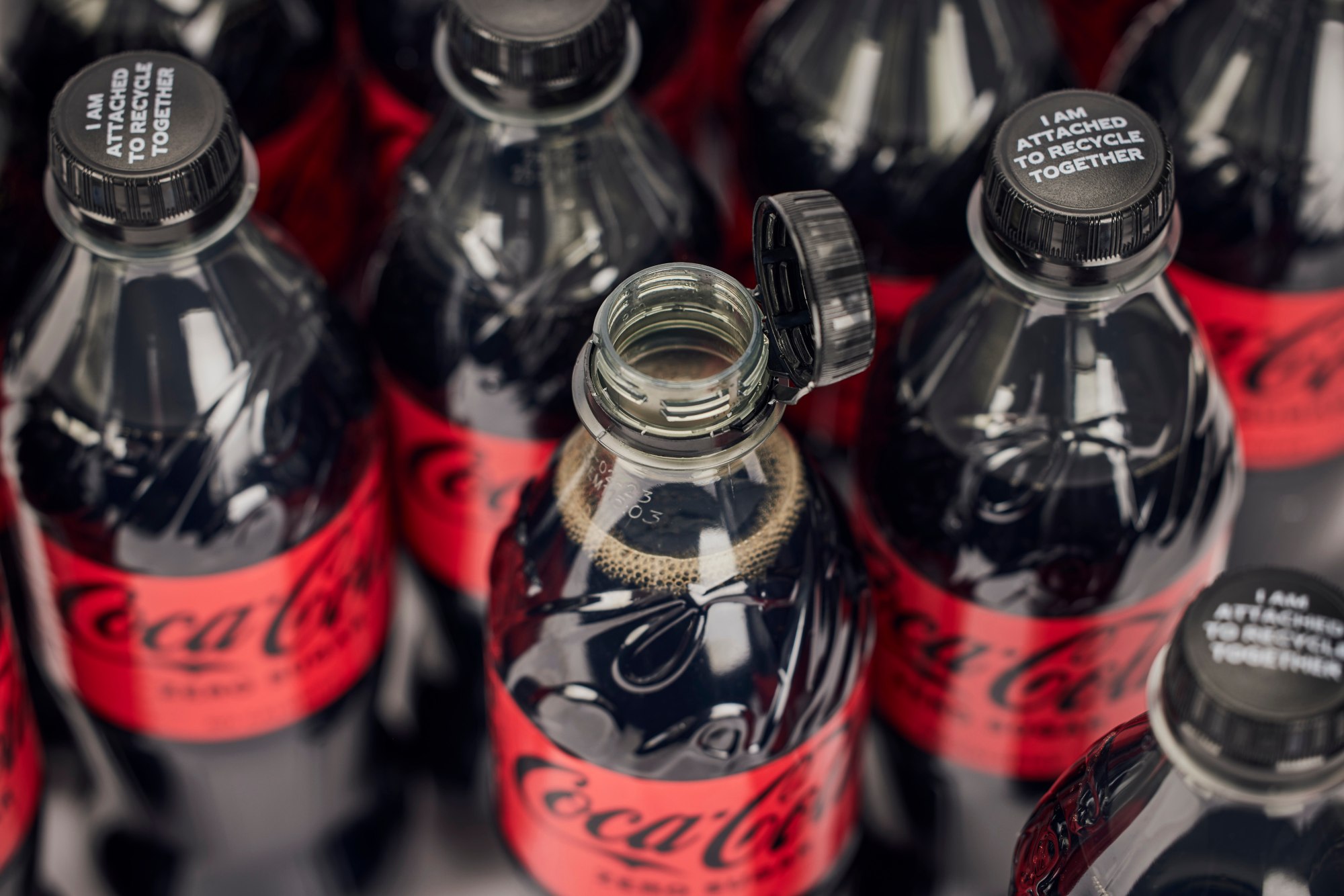
A recent £3m investment has allowed us to convert our existing lines to produce 500ml plastic bottles with attached caps. We’ve also invested £5.8m in a rear door loading facility, which has doubled the number of loading bays at the site, and increased overall capacity by 22%.
This takes our overall investment at the site to £42m since 2017, and we’ve come a long way since then. We’re currently on a journey to gaining a carbon neutral status, and it’s these investments and steps like these that are helping us to make that happen.
I’m proud of the changes that each and every one of the 280 employees has contributed to at Edmonton to reduce emissions so far. The work we’ve put in here will eventually help make a difference across Great Britain in improving recycling rates and, one day, help us to achieve a World Without Waste.
* Excluding labels and caps
Implementing an interoperable DRS across GB
Deposit Return Scheme: T-minus 12 months, by Jim Fox
Originally published on PoliticsHome on 18th August 2022
The topic of sustainability is continually in the spotlight – and rightly so. Droughts and wildfires in recent weeks are, sadly, a stark reminder of how pressing the climate emergency is.
As a business, we’re committed to reducing our carbon footprint and recognise we have an important part to play in taking consumers on this journey with us. One area where we know we have a significant impact, and where we can help to tackle the problem, is through our packaging.
The good news is the food and drink sector has made great strides when it comes to accelerating the use of recycled content in packaging in recent months.
At Coca-Cola Europacific Partners (CCEP) we recently announced the roll-out of attached caps on our plastic bottles, making it easier to recycle the entire package and ensure no cap gets left behind. We’ve increased the use of recycled plastic (rPET) in our 500ml bottles too, which are now made from 100% rPET. This will help to save more than 29,000 tonnes of ‘new’ non-recycled plastic across our operations in Great Britain every year.
And it’s hugely encouraging to see similar steps from others in the sector, contributing to efforts to create a closed loop for packaging.
Part of this means continuing to do all we can to recover more high-quality plastic, and key to achieving this is through the implementation of a Deposit Return Scheme (DRS) where consumers pay a small deposit when they buy a drink in a single-use container and then get the deposit back when they return the empty bottle or can.
We’ve been working with Circularity Scotland to support the implementation of an effective DRS in Scotland, which is due to go live in 12 months’ time. DRS will play a vital role in helping to recover more high-quality plastic to be reused and we continue to work closely with the UK governments to support the introduction of consistent and interoperable schemes across the country.
As a leader in the industry, we recognise that we have a role to play in educating consumers by working collaboratively with our retail customers and with governments to help ensure that the scheme is as effective as possible. If successful, a DRS will deliver significant positive outcomes for the environment and help towards creating a circular economy for packaging.
A truly impactful DRS will only work well if we implement a consistent approach and if the schemes are fully interoperable. It’s important to get it right so that it works for the industry, consumers and, crucially, the environment.
These collaborations with Government and industry partners are essential in helping us to achieve our sustainability goals so that, together, we can create meaningful change, one step at a time.
Back to members home page